Compressed air systems often waste energy because they don’t have a reliable way to manage their capacity. Most of the time, they carry too much capacity to prevent pressure dropping below peak levels. Since this is not always necessary, it can be wasted.
This presents industrial facilities and manufacturers with a problem, as compressed air can cost up to 10 times as much as electricity. The problem is made worse by the difficulties in coordinating multiple compressors to optimize their efficiency.
The CAMLink™ compressed air automation system solves this issue by automatically coordinating all compressors. It can monitor changes in the supply and plant pressures to 0.01 PSI and quickly respond to them by adding or removing compression capacity. This means better regulation of capacity and prevents wasted compression.
Two Options for Small to Medium-Sized Systems for Optimal Compressed Air Management
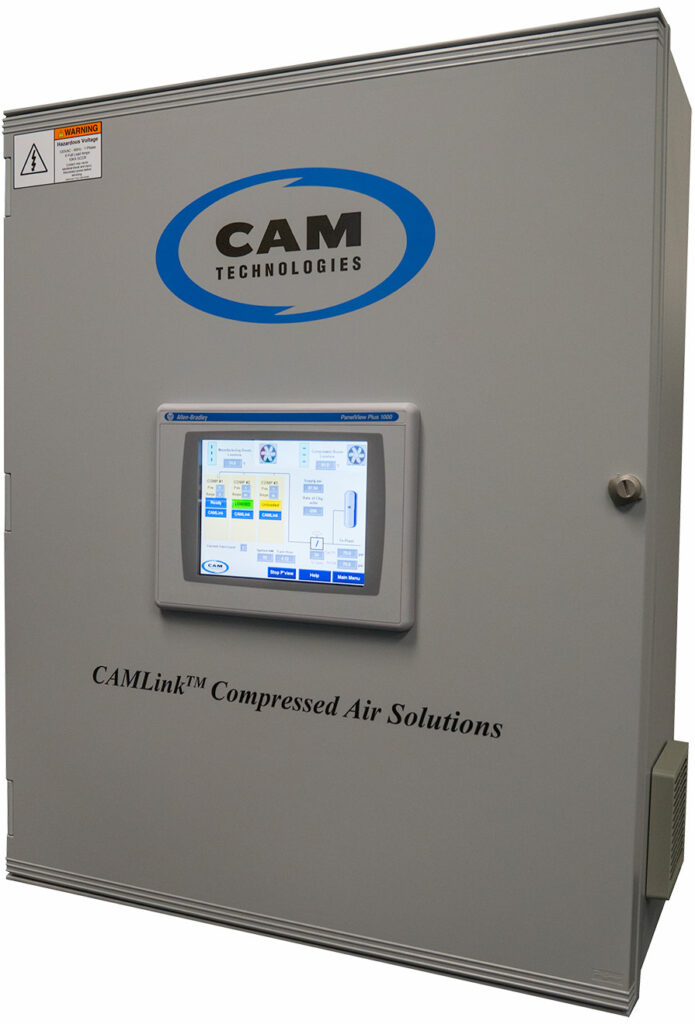
CAM Technologies provides two options for facility managers and engineers to implement into their automation system diagrams:
- CAMLink™ Mini — Designed to support up to six compressors, this mini compressed air automation unit offers superior control and efficiency for optimizing compressed air systems. Depending on the facility’s installed horsepower, these systems can provide fixed or automatic rotation.
- CAMLink™ Advanced — This unit provides the same level of control as the CAMLink™ Mini, but also offers support for centrifugal compressors and Modbus interfaces. It also features advanced compressor management logic.
Benefits of Utilizing CAMLink™ in Your Facility
The features and benefits that the CAMLink™ system offers to plant operators include:
- Allen Bradley Micrologix PLC-based — non-proprietary and easily supported
- 5.7” Allen Bradley Panelview Plus 7 HMI operator interface
- Automation of up to six compressors, even different brands
- Capability to interface with dryers, Demand Expander™, flow meter, and dew-point monitors and miscellaneous alarm inputs
- Single-band pressure control
- Controls rotary screw, reciprocating and centrifugal (CAMLink™ Advanced only) compressors
- 24/7 CAMLink™ Online Service – system data collection and analytics
- 24/7 automated system monitoring and notifications of alarms and preventative maintenance indicators
- Secure client remote access
- Extended warranty on all control components
- Remote training courses for new employees
- Remote support for CAM Technologies engineers
Don’t let wasted capacity hurt the efficiency of your compressed air system. Gain control and operate much more efficiently with CAMLink™ Mini or CAMLink™ Advanced.
Contact CAM Technologies today to learn more.